CCM® OCT Filters Reduce Downtime, Improve Safety, Increase Production
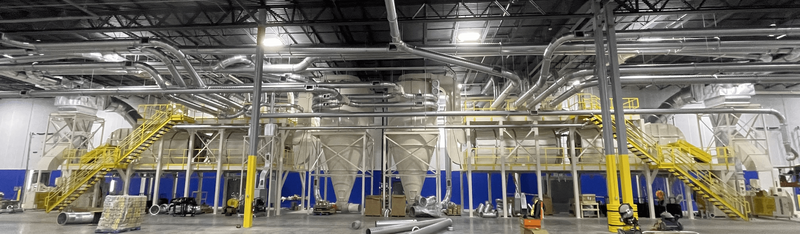
Baghouse and cartridge-style filters have long been the go-to solution for removing dust from manufacturing operations, but there are some significant downsides to this type of dust collector. They require explosion venting, abort gates, sometimes building make-up air, and additional fire protection, in addition to the long and costly downtimes to maintain and unplug them.
Servicing them can take an entire weekend, but many companies in the paper industry are oversold with orders. Some of them are booked well into 2024. They cannot afford to stop production for two or three days and lose hundreds of thousands of dollars while the filter is being properly maintained or unplugged.
“I’ve had a lot of problems in the past where they plug up and you can’t get in to see what’s going on,” said one ERS customer.
Some companies have policies that do not allow employees to enter confined spaces. They must hire out- side crews when their baghouses are up for inspection or maintenance. Even when they can perform this function in-house, baghouses create liabilities that include the use of ladders and cranes.
After a spot fire burned down the baghouse at the customer’s facility, the customer decided to try a different kind of baghouse, but maintenance costs were still cost-prohibitive, with new filter bags costing $25,000 a set plus another $10,000 for labor. These costs were incurred quarterly to properly maintain the unit and keep it running correctly.
In search of a solution, the customer presented this problem to Engineered Recycling Systems (ERS). They wanted something that would be easier to service, less expensive, and not as dangerous. Mike Carver, a Mechanical Engineer by degree and Managing Partner at ERS, recommended the Continuous Cleaning Modular Filter (CCM® OCT). After seeing the drawings and proposal, the customer decided to try it out.
“We set it all up in a weekend and started it up on Monday morning,” the satisfied customer said.
Safety Is Paramount

ERS designed the CCM® OCT filter so that it can be kept safely indoors in a dry environment anywhere in the plant. Since it is not boxed in, the conditions for the explosion are not present. Explosion vents, high-speed abort gates, and expensive fire protection systems are not needed, and if the filter were to catch fire, the sprinkler system would extinguish the fire and the damage would be minimal. Because of its wide-open design, the only thing that would burn is the filter media itself. The media would simply be replaced, and production would continue.
The CCM® OCT filter can also be safely inspected from the ground without ladders or cranes. Unlike traditional filters, you can see inside the unit and monitor it while it is running much like a see-through filter on a vacuum cleaner.
“All you have to do is walk by and you can tell if it’s working,” the customer said. “If there is a problem, you can see it right away. Whereas with a baghouse you have got no idea what is going on inside of it.”
Listening to customer feedback played a significant role in improvements that were made to the filter as it was being developed.
“ERS will come right in and take care of it. It is not like they are asking for a P.O. number,” the customer said. “If there is a problem, they want to rectify it and move for- ward. You do not have to wait weeks for somebody to come in. ERS becomes your partner.”
ERS worked with a major integrated and their consulting firm specializing in fire protection engineering to ensure that the filter met all OSHA and NFPA requirements for non-explosives. Several standard designs resulted from this and the filter was fine-tuned to be compliant with all industry standards and local codes moving forward.
ERS further refined the system so that companies can change out the filter media in-house and have it back in service within minutes resulting in minimal disruption. No special tools are required, and employees do not have to go outside and fight the elements.
“We don’t have to pay to bring somebody else in any- more,” the customer said.
Once sales for the CCM® OCT filter took off, there were no problems getting them insured. Insurance companies came to the facilities to inspect them and approved and certified them every time. Though, in the beginning, some insurance companies were not willing to pre-approve the filters prior to installation, it was found that they were basing that on pre-approval requirements that were written for filters with older technologies that are not applicable to CCM®’s new type of construction and operation. Users are now urging insurers to update their policies to fairly reflect
“Our ERS system meets all codes and insurance companies have approved it across the board,” the customer said. “I will argue with any insurance company and win that argument. They cannot give us an engineering reason why they would not insure it.”
Downtime Cut By 80 Percent
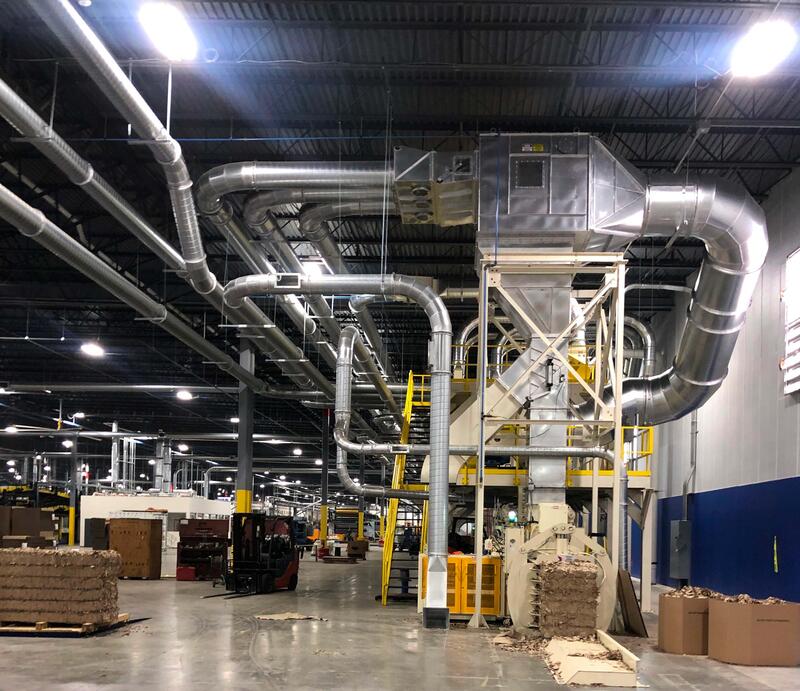
The cost of owning a CCM® OCT filter is less than half the cost of owning a baghouse or cartridge-style filter. Customers can save money and most importantly gain valuable time annually on every unit. Servicing the filter is so quick and easy that downtime has been cut by 80 percent. Instead of having to hire an outside crew for an entire weekend, two people can perform complete preventive maintenance and filter media change out in 2-6 hours de- pending on the size of the unit – and it is all done indoors, without the use of a ladder or special tools. The best dust collector is the one you do not have to think about. With explosion hazards out of the way, simple maintenance, and a window to monitor the internal operation, the CCM® OCT filter is a solution that is engineered to give you peace of mind.
ERS’s satisfied customer went on to install five more units across the Midwest, with a few more in the works. There are currently more than sixty-five fully operating, insured CCM® OCT filters in service throughout the United States, with many more on order.