EV Battery Recycling Solutions separate copper and aluminum from the black mass
Black mass recovery systems from Engineered Recycling Systems (ERS) deliver precision-engineered solutions for extracting valuable metals from electric vehicle (EV) battery waste. These systems are designed to separate copper and aluminum from the black mass — a dense, complex mixture of shredded battery components — without recycling the entire battery. ERS focuses on building custom machinery that enables recyclers to recover high-purity metals while maintaining confidentiality and operational control.
Black mass is the residual material generated during the dismantling and shredding of lithium-ion batteries. It typically contains a mix of copper, aluminum, graphite, lithium compounds, and other residuals. While ERS does not perform the recycling itself, it designs and builds the specialized equipment that enables recyclers to process black mass efficiently, safely, and sustainably.
The recovery process begins with a secure feed system that introduces black mass into the separation line. ERS systems are tailored to handle variable input compositions, ensuring consistent performance across different battery chemistries and formats. Material is conveyed into a proprietary separation chamber where copper and aluminum are isolated using calibrated airflow, density profiling, and mechanical agitation.
ERS black mass recovery systems may include:
-
Air separation units for density-based sorting
-
Magnetic separators to remove ferrous contaminants
-
Sensor-based sorters for conductivity and shape recognition
-
Dust filtration modules to capture fine particles and improve air quality
These components work together to deliver clean metal fractions suitable for resale or refining. The systems are modular and scalable, allowing facilities to configure layouts based on available space, throughput goals, and material types.
Confidentiality is a core feature of ERS’s approach. Many EV battery recycling operations involve proprietary chemistries, sensitive data, or strategic partnerships. ERS designs its black mass recovery systems with discreet architecture and secure integration protocols, ensuring that customer information and process details remain protected.
Dust control is critical in black mass processing. ERS integrates high-efficiency filtration systems — including optional CCM® OCT filters — to capture airborne particles and recover trace metal fines. These features support regulatory compliance, improve workplace safety, and contribute to higher total recovery rates.
ERS black mass recovery systems support a wide range of input materials:
-
Shredded lithium-ion battery components
-
EV battery black mass from dismantling lines
-
Residuals from cathode and anode separation
-
Mixed metal fines from battery recycling streams
-
Copper and aluminum fragments from battery terminals and foils
Each system includes intuitive control panels, maintenance access points, and wear-resistant components designed for long-term reliability. Safety features include interlocked panels, emergency stops, dust containment, and acoustic dampening — all engineered to meet industrial compliance standards while protecting personnel.
Process intelligence is built into every ERS system. Programmable logic controllers (PLCs) and real-time monitoring tools allow operators to adjust separation parameters, track throughput, and optimize performance. Remote diagnostics and cloud-based analytics ensure uptime and help facilities adapt to changing material streams.
ERS supports customers with full lifecycle services — from system design and layout planning to installation, training, and optimization. Their engineering team works directly with processors to define recovery goals, configure equipment, and ensure consistent performance. Technical support and upgrade paths are available as battery technologies evolve or throughput increases.
The economic impact of black mass recovery is significant. With demand for copper and aluminum rising in the EV and renewable energy sectors, processors equipped with high-efficiency systems can capture more value from battery waste while reducing disposal costs. ERS systems help facilities meet environmental benchmarks, improve ROI, and strengthen their competitive position in the metals recycling market.
In addition to metals recovery, these systems contribute to broader operational efficiency. By reducing the volume of waste sent to landfill, facilities can lower tipping fees, minimize regulatory exposure, and improve their public sustainability profile. Clean separation also improves downstream material quality, reducing the need for secondary processing or manual sorting.
ERS black mass recovery systems are trusted by recyclers, battery manufacturers, and energy storage companies across North America and Europe. With proven results in demanding applications — from EV battery dismantling to cathode-anode separation — ERS equipment delivers long-term value, reliability, and support.
In short, these systems are engineered to help processors recover more metal, reduce waste, and stay competitive in a resource-conscious industry. With modular design, advanced separation technology, and full lifecycle support, ERS black mass recovery systems turn complex battery scrap into clean profit.
Get in touch
Engineered Recycling Systems, LLC. The industry leader in dust collection, metal separation and trim removal systems – comprised of the industry’s top engineers and system integrators, incorporating the finest equipment technology, expansive industry knowledge and expertise, and enabling ERS to provide customers with the latest and most innovative integrated systems in the world.
+1 770-954-8780
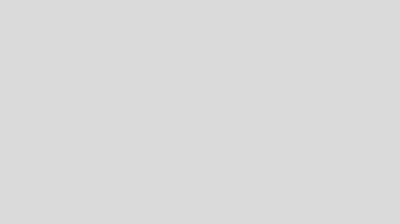